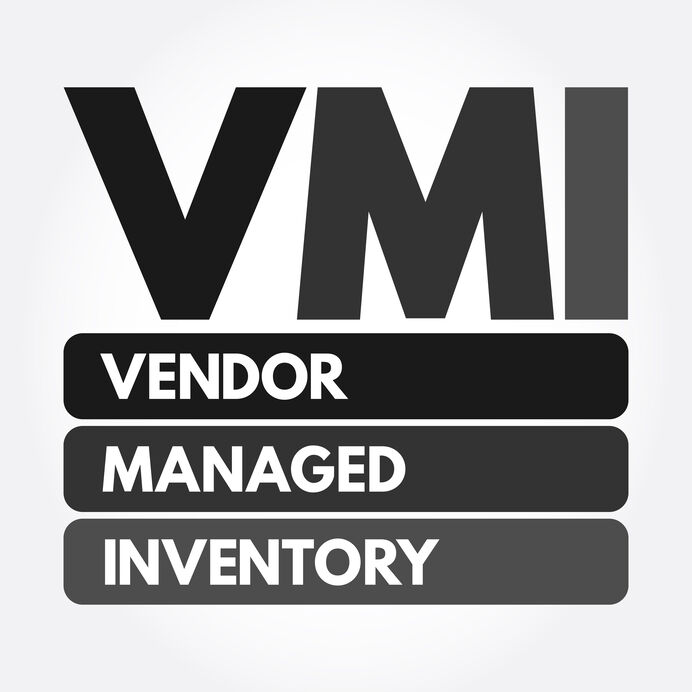
Vendors and customers care about supply chains, tauagavale? Customers want to make sure they get what they ordered on time and in good condition, and they also want to make sure they have enough of what they need to do their work– at all times. Vendors obviously want to sell products to make money, but they, foi, care about satisfying customers’ needs. Ae uma ane, a vendor who doesn’t meet the needs of a customer won’t be in business very long. Faatasi ai ma lena mea i le mafaufau, what are some benefits of a custom developed VMI program?]VMI stands for “vendor managed inventory.” This is where the vendor is put in charge of a customer’s inventory. What are some benefits to this arrangement?
How VMI Relationships Help Your Company
Tulaga tasi, a VMI relationship means that the vendor is in charge of replenishment, so they can adjust inventories in response to customer demand. This helps deal with seasonal changes, special promotions and new initiatives in a proactive manner. Ultimately, this lowers carrying costs and eliminates inefficiencies. Having a streamlined VMI process in place can reduce the frequency of last-minute orders, reduce the overall number of orders and reduce returns as well.
Le isi, VMI utilizes data analytics to better understand actual demand– this helps people gain insight into the marketplace and can allow for expansion, foi. Want to improve performance and build a stronger relationship with customers? Gain data insights thanks to your VMI relationship.
Mulimuli ane, if you want to be in closer collaboration with customers, VMI is the way to go since the program develops through cooperation– expect superior service and on-time delivery and even improved sales figures. VMI is kind of like having a big brother watching out for you, helping guide you and being there for you in times of need.
For those customers looking for a more calculated inventory fulfillment option, Eagle Alloys offers a VMI program designed to fit your specific needs. Our team will work closely with your organization to help identify alloy requirements and scheduling to ensure that your material is never in short supply. Please call 800-237-9012 to discuss Eagle Alloys’ VMI program.